The Supply Chain Was Messy. Then COVID Happened
The Great Supply Chain Disruption didn't start with the pandemic. The US-China trade war disturbed the Global Supply Chain; extreme weather amplified its vulnerabilities. Then, COVID hit.
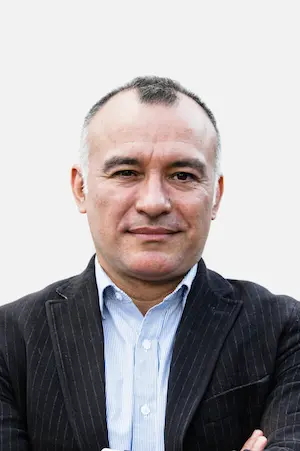
Discussions about the supply chain dysfunction usually begin with COVID-19. However, the tsunami of freight we see today has roots in the US-China trade war. A unique character to illustrate the domino effect of issues is the cargo container.
Under normal circumstances cargo containers, called "the workhorse of globalization," wouldn't make for an interesting story (at least not as the protagonist). But these are not ordinary times. Even as the world produces more cargo containers than ever before, farmers in Ohio can't find them to ship soybeans to Asia. And they are not alone: most of the things on your Christmas shopping list will spend an unusual portion of their journey looking for a container or stored in one.
In 2019, the world traded $4.93B in cargo containers, with China ($1.81B), Guyana ($510M), and the United States ($412M) sharing 54% of global exports. In the first three-quarters of 2021, China alone exported $14.3B. Although this increase partially reflects a rise in prices, the industry will produce a record of 5.2M twenty-foot equivalent units (TEUs). Between January and September 2021, China International Marine Containers (CIMC) sold 1.14M TEUs, a year-on-year increase of 219%.
The world has more containers than ever before, but many of them are in the wrong places. Although the clogged stream of containers in ports exposes systemic issues with the logistics chain, we can trace the first cracks in the Just-in-Time manufacturing back to when the world's two largest economies were engulfed in a trade battle.
The U.S.-China Trade War
Just-in-Time manufacturing works on the assumption of an accurate demand forecast and reliable transportation. However, in 2018-2020, a trade war between the two largest economies (22% share of global trade) increased the uncertainty of planning and logistics on a scale never seen before.
On July 6, 2018, U.S. tariffs on $34B of Chinese imports went into effect. The United States imposed a 25 percent tariff on semiconductors, among other goods. During this conflict, each battle used a particular rationale and targeted different products. At the end of the tit-for-tat escalation, the U.S. had imposed tariffs on 6,094 goods. Of all the intermediate inputs the U.S. imports from China, only 13 percent escaped punitive US duties. China, on the other hand, targeted commodities and final products.
Overall, U.S. imports from China declined by $88 billion in 2019, as compared with 2018. A sharp drop in electrical machinery and equipment, machinery and appliances and furniture and vehicles parts drove the decline. This fall saw the most significant annual decline in U.S. imports from any country, except for Canada ($112B) after the 2008 financial crisis.
The US-China trade war had immediate effects on trade and, as a consequence, the demand for containers shifted. When the final truce came in February 2020, imports of containers in the U.S. had dropped by 55.5% while increasing in countries trading commodities with China. Overall, container exports from China fell 72.6%.
Modern products are puzzles of sophisticated pieces that require specialized equipment to make. It isn't practical for one company to produce everything by itself. With the adoption of Just-in-Time manufacturing, companies outsource production and operate with low inventory levels, freeing up capital.
Consider, for example, cars. A vehicle has about 30,000 parts made with various materials and processes. Carmakers rely on suppliers who focus on just one group of features, and those suppliers rely on others centered on one component. This system gives automakers the flexibility to use the latest technology (for example, touchscreens) at the lowest cost. But it also makes manufacturers depend on parts produced elsewhere (for example, semiconductors) to complete a vehicle. If most of your suppliers are located in an area connected by only a few logistics hubs, the risks for disruption are higher.
Change in Vehicle Parts imports by market (2018 - 2019)
The U.S.-China trade war created volatility in supply and demand of Global Value Chains, generating an unexpected shift that stressed global logistics.
Then came COVID-19...
The pandemic
In February 2020, shipping companies, relieved by the end of the trade war, entered into another crisis. The pandemic produced a drastic shift in consumption, and with it, a domino effect down the supply chain. At first, shipping companies reduced their already low estimates of new containers, leaving empty ones uncollected in some terminals due to COVID-19 restrictions.
Two new trends in trade developed in merely six months: the massive need for medical equipment (PPE, ventilators, and vaccines) and the acceleration of the digital transformation of the economy. Suddenly, millions of people worked and studied from home, bought furniture online, and used the money saved from travel expenses to buy laptops and cellphones.
A year after the beginning of the pandemic, laptop imports in the United States were up 85%, cellphones 48%, and headphones 615%. China, the first country to recover, was uniquely positioned to take advantage of the dramatic shifts in global demand.
Later, other countries in Asia recovered. But stressed cargo terminals in the U.S. could not send containers back to Asia on time, expanding the backlog. The shift in demand created an incentive for carriers to prioritize shipments out of China. As a result, some cargo containers didn't wait for U.S. exporters to load their goods and instead prioritized more profitable businesses in Asia, leading to an increase of empty containers in U.S. ports.
Products waiting for containers to take them to their destination are delaying economic activity and intensifying the disruption in the supply chain. The domino effect of the supply chain breakdown began with geopolitics. With more containers than ever, moving them around the world has gone from Just-in-Time to Just-in-Possible.